Introduction
Knife gate valves are a go-to solution for isolating flow in industrial systems handling slurries, viscous fluids, and abrasive media. However, like any mechanical component, they can face performance issues over time. In this blog, we’ll discuss five common problems with knife gate valves and provide practical solutions to ensure optimal performance.
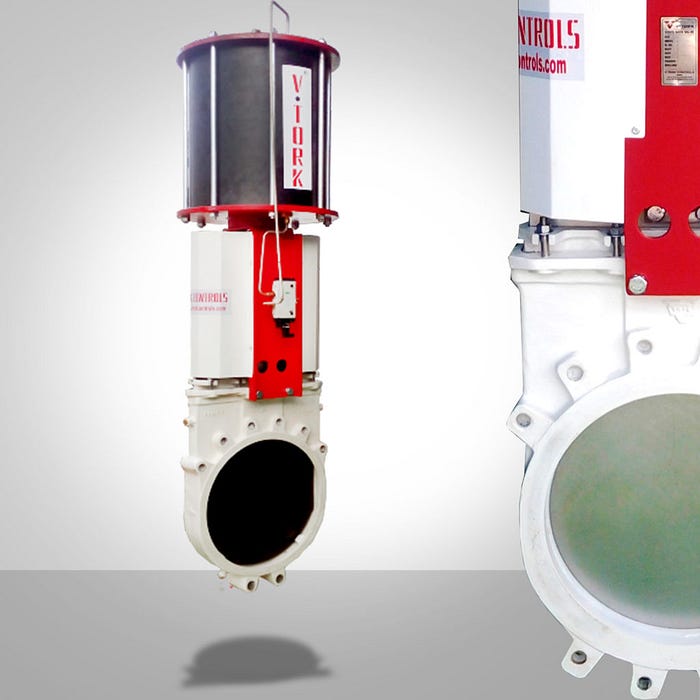
What are the five common problems with knife gate valves?
- Leaking around the valve
- Gate jamming or sticking
- Excessive wear and tear
- Actuator failure
- Inadequate flow control
Now lets dive deep into these problems faced and its respective solutions
1. Leakage Around the Valve
Cause:
- Worn-out seals or improper sealing surfaces.
- Corrosion or build-up of debris on the gate or seat.
Solution:
- Regularly inspect and replace seals as part of maintenance.
- Opt for resilient-seated knife gate valves like V-TORK’s U-Series for enhanced sealing performance.
- Ensure the valve’s materials are compatible with the media to prevent corrosion.
2. Gate Jamming or Sticking
Cause:
- Accumulation of solids or debris in the valve body.
- Misalignment of the gate or actuator.
Solution:
- Choose valves with a self-cleaning design, such as V-TORK’s B-Series, to minimize debris build-up.
- Regularly flush the valve and system to remove accumulated solids.
- Check for proper alignment during installation and actuator setup.
3. Excessive Wear and Tear
Cause:
- Exposure to abrasive or corrosive media without suitable material selection.
- Prolonged operation under extreme conditions.
Solution:
- Use knife gate valves made from durable materials like SS316, CD4MCu, or CN7M for abrasive or corrosive environments.
- For heavy-duty applications, select slurry knife gate valves with metal-to-metal seating for superior durability.
4. Actuator Failure
Cause:
- Overloading or improper sizing of the actuator.
- Lack of lubrication or maintenance.
Solution:
- Match the actuator type (manual, pneumatic, or electric) and size to the application requirements.
- Regularly lubricate moving parts to prevent wear.
- For automation, choose V-TORK valves with advanced actuators for reliable performance.
5. Inadequate Flow Control
Cause:
- Incorrect valve sizing for the application.
- Erosion of the valve gate or seat, reducing sealing efficiency.
Solution:
- Work with experts like V-TORK to select the right valve size and material for your application.
- Conduct regular inspections and replace worn components promptly.
Preventative Maintenance Tips for Knife Gate Valves
- Inspect Regularly: Check for wear, corrosion, or debris build-up.
- Flush the System: Periodically clean the valve and piping to prevent blockages.
- Replace Worn Parts: Timely replacement of seals, seats, and other components extends valve life.
- Use Compatible Materials: Ensure the valve materials match the media and operating conditions.
Why V-TORK Knife Gate Valves Are Built to Last
At V-TORK, we design and manufacture knife gate valves to withstand the toughest conditions. Here’s why industries trust our solutions:
- Durable Materials: Built with high-grade metals like SS316, WCB, and CD4MCu.
- Innovative Design: Self-cleaning features to prevent jamming and wear.
- Customization: Tailored solutions to meet unique industrial challenges.
Conclusion
Understanding the common problems with knife gate valves and their solutions can save industries time, money, and operational downtime. With proper maintenance and high-quality products, these challenges can be effectively managed.
For reliable, durable, and efficient knife gate valves, trust V-TORK CONTROLS — your partner in industrial valve solutions.
Explore our range of knife gate valves today!
https://vtorkcontrols.com/contact/ | https://vtorkcontrols.com/products/